Warehouse Management System WMS – Warehouse Management System includes software and processes that allow organizations to control and manage warehouse operations from when goods or materials are in stock until they are shipped.
1. What does the Warehouse Management System do?
Warehouses are central to manufacturing and supply chain operations because they contain all the materials used or produced in those processes, from raw materials to finished products. The purpose of a WMS warehouse management system is to help ensure goods and materials move through warehouses in the most efficient and cost-effective manner. A WMS handles many of the functions that enable these movements, including inventory tracking, picking, receiving, and shipping.
WMS also provides visibility into an organization’s inventory at any time and place, whether on-site or in transit.
2. Where does the WMS Warehouse Management System fit into the supply chain?
Supply chains can only function as quickly, accurately and efficiently as warehouse processes allow. WMS plays an important role in supply chain management by managing order fulfillment processes, from receiving raw materials to shipping finished products.
For example, if raw materials are not received properly or parts are lost in the warehouse, the supply chain can be slowed down or disrupted. WMSes are important in ensuring that these processes run smoothly by tracking inventory and ensuring that goods are properly stored and sorted, as well as shipped and tracked correctly.
A WMS is often used with or integrated with other related systems, including an ERP , a transportation management system (TMS) and an inventory management system.
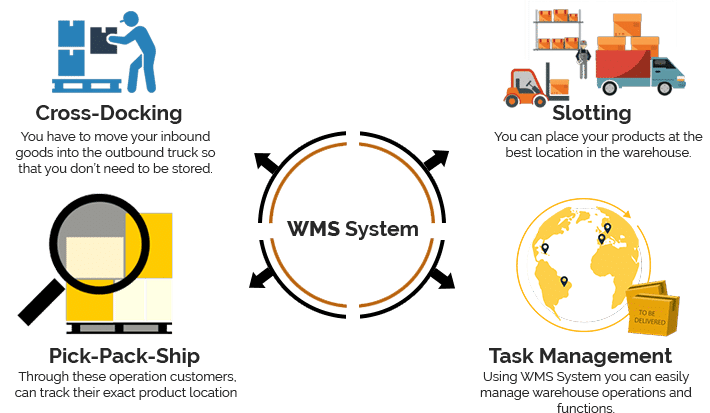
3. Types of warehouse management systems
Warehouse management software comes in various and methods of implementation, and the type often depends on the size and nature of the organization. They can be stand-alone systems or modules within a larger ERP or supply chain execution suite.
WMSes can also vary widely in complexity. Some small organizations may use a series of hardcopy documents or simple spreadsheet files, but most larger organizations – from small and medium businesses (SMBs) to corporate companies – use complex WMS software. Some WMS setups are specifically designed for the size of the organization, and many vendors have versions of the WMS product that can scale to different sizes of organizations. Some organizations build their own WMS from scratch, but it is more common to deploy the WMS from an established vendor.
A WMS can also be designed or configured for the specific requirements of the organization; e.g. suppliers e-commerce can use WMS which has different functions than a traditional retailer. In addition, a WMS can also be specifically designed or configured for the types of goods the organization sells; for example, a sporting goods retailer will have different requirements than a grocery chain.
3.1. Features of warehouse management system
- Design the warehouse, allowing organizations to customize workflow and picking logic to ensure that the warehouse is designed for optimized inventory allocation. WMS sets up bin grooves to maximize storage space and account for seasonal variations in inventory.
- Inventory tracking , enabling the use of an advanced tracking system and automatic identification and data acquisition (AIDC), including RFID and barcode scanner to ensure that goods can be found easily easily when they need to move.
- Receipt and storage, which allows inventory to be stored and retrieved, usually with a pick-to-light (a system that uses light modules to indicate to the manager the exact location of goods in the warehouse) or pick-to-voice technology (voice product recognition) for warehouse staff to help locate goods.
- Picking and packing goods , including area picking, wave picking, and bulk picking. Warehouse workers can also use batch zoning and task interleaving functions to most efficiently guide picking and packing tasks.
- Shipping , allows WMS to send a bill of lading (B/L) in advance of shipment, generate packing lists and invoices for the shipment, and send pre-shipment notices to recipients.
- Labor Management , which helps warehouse managers monitor worker performance using key performance indicators (KPIs) that show workers performing above or below standards.
- Manage the yard, assist the truck driver to go into the warehouse to find a suitable loading dock. The use of more sophisticated dock and dock management allows for cross-linking and other functions of inbound and outbound logistics.
- Reports , helping managers analyze warehouse performance and find areas for improvement.
Cloud-based WMS:
Warehouse management systems, along with other enterprise systems like ERP, start out as systems that are run on an organization’s on-premises servers. This paradigm has been changing and cloud-based WMSs are more popular as organizations realize the benefits of running systems in the cloud.
The key feature of a cloud-based WMS compared to a traditional on-premises system is that the software is hosted and managed by the WMS provider or cloud service provider. This removes the burden of installing, managing, and upgrading systems from the organization’s IT department.
Because they are easier to install and less expensive to manage, cloud-based WMSs tend to be favored by small and medium-sized businesses. Larger enterprises often deploy WMS on-premises because they need highly customized systems that meet their specific industry requirements, and they have sufficient resources to manage IT requirements.
Advantages of cloud-based WMS include:
- Perform faster: Traditional on-premises WMSs can often take months to deploy, while cloud-based WMS deployments can be completed in weeks, depending on complexity. This means that organizations have a faster path to positive ROI and can take advantage of cloud WMS capabilities sooner, which is a huge boon in the fast-paced modern economy. speed.
- Upgrading is less complicated: The cloud-based SaaS for WMS deployment model includes regularly scheduled upgrades where all updates and configurations are handled by the vendor. This means that organizations always use the latest version of their software and spend minimal time and resources managing each upgrade.
- Cheap: Cloud-based WMSs do not require hardware, software, and IT administrators to manage them. As a result, they have lower upfront and sometimes ongoing costs than on-premise systems. They also require no customizations or modifications, which can be costly for on-premises systems. On-site system upgrades can also be expensive, as they can involve reinstalling and reconfiguring software and, in some cases, hardware upgrades.
- Ability of extension: Cloud-based WMSs can scale quickly as organizations grow and supply chains become more complex. They are also more flexible and can be reconfigured as business requirements or market conditions change.
Disadvantages of cloud-based WMS include the following:
- Long term costs: While cloud-based WMSs typically have lower upfront costs than on-premises systems, paying for a monthly or yearly license can be more expensive in the long run. Organizations may also incur additional costs to deploy new modules or premium support packages.
- Customization: SaaS WMS software is generally non-customizable, making it less suitable for organizations that need to modify the software to meet their specific processes or industry requirements.
- Updates: Cloud-based WMSs are regularly updated for all customers. While this ensures that the system is always up to date, it may require frequent process changes by the customer to update new software, and users may need retraining each time the software is updated if changes are important.
All major WMS vendors (IBM, Microsoft, Oracle, and SAP) offer a variety of deployment options, including cloud-based systems. Predominantly cloud-based or cloud-based WMS providers include Fishbowl, HighJump, and SnapFulfil only.
4. Benefits of warehouse management system
Although a WMS is complex and expensive to implement and operate, organizations reap many benefits that can justify the complexity and cost.
Implementing a WMS can help an organization reduce labor costs, improve inventory accuracy, improve flexibility and responsiveness, reduce errors in picking and shipping, and all. improve customer service. Modern warehouse management systems work with real-time data, allowing an organization to manage the latest information on activities such as orders, shipments, receipts, and any “movements” of goods.
WMS and IoT:
Connected devices and sensors in products and materials help organizations ensure they can produce and ship the right amount of goods at the right price to the right place at the right time. All these capabilities have become cheaper and more common thanks to IoT.
Such IoT data can be integrated into a WMS to help manage product routing from point of receipt to endpoint. The integration allows organizations to develop a pull-based, rather than push-based supply chain. A traction-based supply chain is driven by customer demand, which allows an organization to be more agile and responsive, while a traction-based supply chain is driven by long-term predictions. about customer needs.
Address: 27 Xuan Quynh, Gia Hoa Residential Area, Phuoc Long B Ward, City. Thu Duc, HCMC
Hotline: (028) 3620 8179 / 3620 8176 / 3620 8177
Fax: (028) 3620 8178
Mail: info@vuletech.com
—————
Follow VULETECH at:
► Youtube