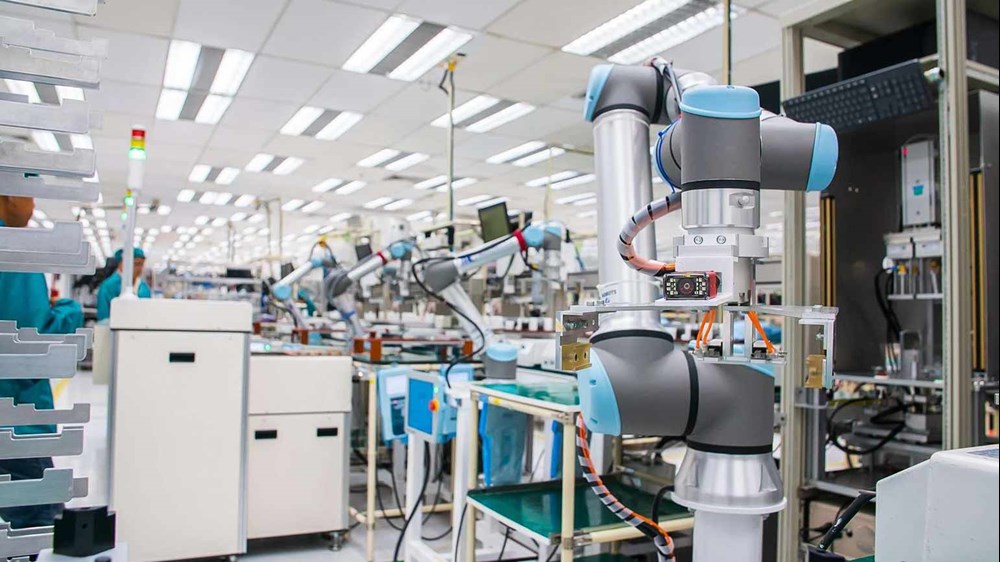
Universal Robots (UR) collaborative robots (cobots) are seen as a key element in successful electronics manufacturing deployments globally. Each implementation has its own characteristics, but the overall results are clear; productivity increases, quality results are improved, human error in repetitive tasks is reduced, and working conditions are improved.
This article will focus on how the UR robotic arm has emerged as a powerful resource to assist electronics manufacturers facing severe business challenges such as demand spikes, shortage of skilled labor, high mix/low volume production (variety of products, easy to adapt but small quantity) and shortage of floor space in production facilities.
Automating the repetitive touch screen testing process with the UR3 cobot helped KOYO ELECTRONICS INDUSTRIES CO., LTD. 31% increase in productivity.
When Koyo Electronics Industries Co., Ltd. Seeing a spike in demand for its car’s touch panel, the manufacturer responded by reallocating workers from manual post-production checks to resolving bottlenecks. in other place. That decision ultimately led to a shortage of skilled labor in the repetitive touch-panel testing processes at the end of the line.
Koyo needed to deploy an automated robot that could handle a wide range of impact forces suitable for touchscreen inspection applications, which could be safely deployed alongside humans without the need for protective barriers. and all must be in compact form to avoid significant changes to existing lines. The company chose Universal Robots UR3 robotic hand, with built-in force level adjustment, multiple safety features designed to meet safe human-robot cooperation and save usable space .
Productivity INCREASE 31%:
The end result was amazing: The UR3 implementation increased productivity at Koyo by 31%. The number of people needed to handle touch panel testing tasks has been halved from two to one, helping workers focus on more ergonomic, value-added tasks including operated the cobot and the company achieved an ROI in just twelve months.
When the UR3 robotic hand touches the touch panel with a stylus without finding any errors, an “OK” message will appear and the green signal tower light is activated. If an anomaly is detected, the message “NG” will be displayed and the red signal tower light will light up with a continuous buzzer sound. As a result, the person in charge is immediately alerted to the anomaly and can respond.
“Our company can not only improve productivity by allocating resources to another production process, but the experience from implementing this robot has given great confidence and hope for the development in the future. future.”
MR KATSUHIKO NAKATANIDeputy General Manager of Manufacturing Division of Koyo Electronics Industries Co., Ltd.
To keep pace with the massive growth in demand for its products, Melecs EWS sought to automate the end-of-line packaging process for its line of small, circular printed circuit boards. Requiring manual operation, spanning three shifts, packing was a monotonous task that had to be completed in a 5-6 second timeframe for each module. Lured by the affordable price and accessibility of the UR robotic arm, Melecs deployed a cobot UR5 to take on these ergonomic tasks.
TWO MILLION COMPONENTS PACKED WITH NO ERROR, FOLLOWING CYCLE TIME:
Final result? Melecs has increased throughput in its packaging operations by 25%, eliminating bottlenecks in production and freeing workers from time-consuming and unorthodox tasks. The robot packs about two million components a year without error, despite having to operate in strict cycles.
A worker places a group of printed circuit boards in the work area of the UR5. The learning robot then scans the three circuit boards with a laser scanner. The cobot’s custom trimmer picks up a circuit board on each tip and then places all three boards simultaneously in a tray. When the tray is full, the robot arm will pack it into the box using the vacuum folding head. When the box is filled, the robot arm closes the lid.
“The robot ran perfectly smoothly over three shifts and we surmise they will pay off within 18 months. Cobot UR is a great addition to our automation strategy and we will definitely include them in future projects.”