ROBOT COOPERATION IN HEALTH INDUSTRY
As medical product life cycles shorten, collaborative automation provides agile manufacturing operations. Universal Robots’ robotic arms can be used to maximize productivity and ensure consistent quality—and can be quickly redeployed to new production lines. Collaborative robots are used throughout the industry to feed machines and conveyors; precision assembly of devices and products; and equip and pack the goods into boxes, cartons or pallets.
Collaborative robots help you reduce the risk of contaminating humans during rigorous environmental sanitation processes. The UR collaborative robotic arm can be used to handle and assemble precision medical or implantable devices under sterile conditions. Robots can also help displace workers from material handling jobs in dusty, noisy and high-vibration environments, allowing them to move into higher-value jobs. And with the UR+ certified image acquisition system, the collaborative robot can conduct detailed quality checks.
Thanks to its easy deployment, setting up robots for medical applications is often measured in hours or days, not weeks. The light-weight collaborative robot arm can be easily moved from process to process on a mobile trolley, and a single robot can often handle multiple machines.
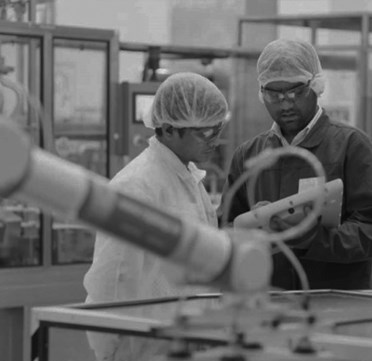
ADVANTAGES OF COLLABORATE AUTOMATIC PROCESS
Productivity
Increase productivity by optimizing equipment and worker utilization. Collaborative robots can work reliably around the clock without breaks, producing higher quality products and minimizing waste. And often get a return in less than a year
FLEXIBLE
Adapt quickly and easily to new products, even low-volume or fast-shifting jobs. The collaborative robotic arm can be programmed and redeployed in the home and can even be mounted on a trolley for increased mobility.
QUALITY
Repetitive tasks that workers do not want to do, because their concentration decreases after many hours performing the same process. Collaborative robots can reliably perform sophisticated assembly and load and unload machines continuously for higher quality and reduced waste.
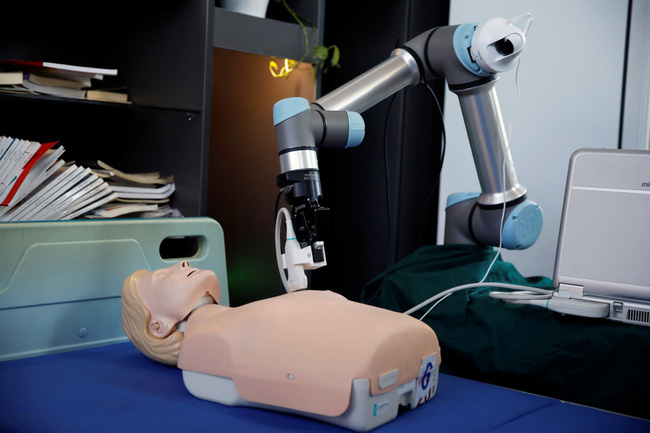
Application of Universal Robot to collect blood samples at COPENHAGEN University Hospital
STORY:
The two UR5 robots have now optimized the handling and sorting of blood samples for analysis at Copenhagen university hospital in Gentofte. This solution allows the laboratory to maintain its goal of delivering more than 90% of results within 1 hour despite a 20% increase in sample arrivals for analysis.
Problem:
Copenhagen University Hospital in Gentofte, Denmark, wanted to find out how collaborative robots could become a cost-effective solution that automates the manual sorting of blood samples for four different pathways for further analysis. . The robot must be placed in a space-constrained area of the laboratory, where larger, automated batch loading machines are not an option. The hospital lab wants technicians to be able to interact with the robot and easily intervene if the process requires human intervention. Faced with a 20% increase in blood sample arrivals to the lab, management also sought to maintain the lab’s goal of having 90% of all blood samples analyzed within an hour without the need for additional staff. .

SOLUTION:
Universal Robots’ collaborative robotic arms can operate barrier-free right next to humans – a radical change from traditional industrial robots that are always fixed in a safe area. Their interactive design makes it easy to set them up for a new task, and their built-in safety system allows the UR robotic arm to automatically stop working if it encounters an object or person in its path. These features are important to the Copenhagen laboratory:
“All the blood samples come to a conveyor belt in one corner of the lab, with no room to put up a safety fence. We needed an inherently secure, easy-to-use solution that could respond to visual guided programming, quickly retrieve, classify, and load samples into the import module for analysis. Copenhagen University Hospital’s chief physician, Steen Stender, who has now deployed two UR5 robots.
The UR robot first takes a sample and places it in the barcode scanner. A CCTV camera takes a color image of the screw cap and the robot is instructed to place the sample in one of four different racks by color. The second robot takes the rack samples and places them in the feeder for centrifugation and analysis. The robot handles approx. 3,000 samples per day, 7-8 tubes per minute.