COBOT PERFORMANCE OF AUTOMATIC PACKING AND PACKAGING
Simplify material handling, packaging, unloading/palletizing, crate picking, labeling, and placement processes with collaborative robots. Free workers from repetitive work and heavy lifting by using a series of lightweight collaborative robotic arms to automate material handling tasks. Automation helps you deal with rising new product packaging costs and shortened product life cycles, making it easier to meet peak season demand despite labor shortages.
Collaborative robots with innovative grippers, computer image acquisition, and machine learning systems can pick up a variety of objects in unstructured environments, such as crates or bags. Easy-to-integrate SKU scanning and the ability to pick up bags or products of nearly any size or shape help with e-commerce, order fulfillment, warehousing, logistics, and supply chain operations simpler, faster and more efficient.
The intuitive, easy-to-program interface makes the UR robotic arm the perfect choice for low volume applications as well as high repeatability tasks. You can fully reprogram and redeploy the robot as needed in your operations. Thanks to its compact and lightweight design, even with changes in your workflow, you can quickly and easily deploy the material handling robotic arm to new systems.
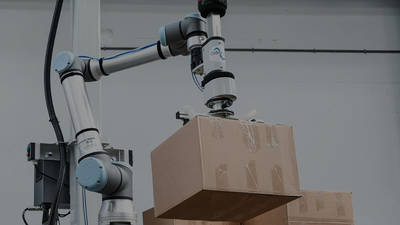
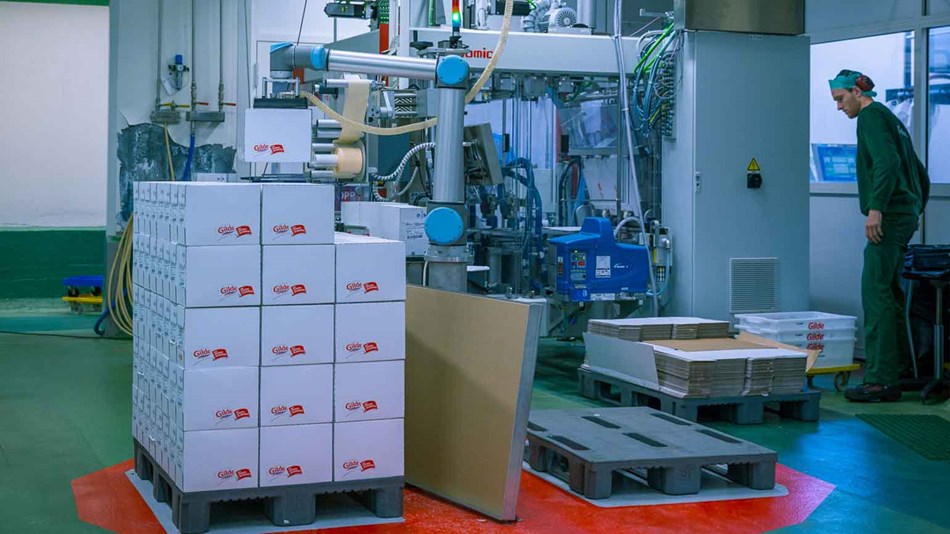
Advantages of Universal Cobot
- The UR robots can be used in most packaging and palletizing applications. Our space-saving robots can also be quickly reprogrammed and used with a variety of machines.
- Reduce inconvenient, repetitive jobs for workers.
- With Universal Robots’ robotic arm, you can empower your workforce to do more important work.
- Reduce your operating costs. Universal Robots gives you all the advantages of robotics automation, without the traditional costs associated with robot programming, setup, and security staffing. The average payback period is 195 days. This is the fastest timeframe in the robotics industry.
- During peak seasons, Universal Robots robots can operate 24/7, bringing unlimited productivity to your business. The robot can be deployed and reprogrammed as needed to change between tasks and applications if necessary.
- All collaborative robots from Universal Robots are IP-54 certified. The robot will need protection when working in corrosive liquid environments.
Clearpack leverages UR+ to design an innovative queuing solution
Story:
Singapore-based Clearpack is a leading supplier of packaging automation solutions with customers in Southeast Asia, China, India, the Middle East and Africa. Upon discovering cobot maker Universal Robots+ (UR+), a global product platform featuring certified third-party plug-and-play solutions for Universal Robots (UR) cobots, Clearpack quickly can design a safe, compact and easy-to-use palletizing solution that includes the Cobot UR10 and SKF Motion Technologies’ LIFTKIT, a global supplier of linear motion components. This has helped many Clearpack customers in the FMCG sector optimize their warehouse space and enjoy a fast return on investment (ROI) on their investment.
Problem:
Many times, manufacturers fail to take into account space for automated palletizing, a process that automatically stacks product crates on pallets, when planning production floor layouts. This presents them with a spatial challenge. Committed to developing smart and innovative solutions, Clearpack aims to design an efficient cargo handling system for its customers, a system that is safe, compact, flexible and easy to use, while Time allows businesses to make maximum use of warehouse storage space.
Solution:
Clearpack is familiar with Universal Robots (UR), which previously used UR cobots to develop packaging and case erection solutions for its customers. The partnership proved successful, leading the team to UR once again to design a queuing solution, this time with the help of the UR+ ecosystem and SKF Motions Technologies’ LIFTKIT.
Flexible:
- One of Clearpack’s main considerations when choosing UR is its open platform, which means that end users can program the application flexibly on their own.
Easy to use:
- Clearpack must ensure that the solution is easy to implement so that its customers in the FMCG sector can quickly adapt to it. UR’s user-friendly machine interface has facilitated this, and the cobot’s collaborative nature allows it to work collaboratively with everyone.
Safe:
- For Clearpack, a risk assessment is an integral part of any project feasibility study as they work with many of the top multinational companies that have high safety standards. With the right application and the right accessory design, the team was able to put a system together without the need for a safety guard. Safety protection is often required when deploying bulky traditional industrial robots, resulting in additional costs for installation and changes to plant layouts.
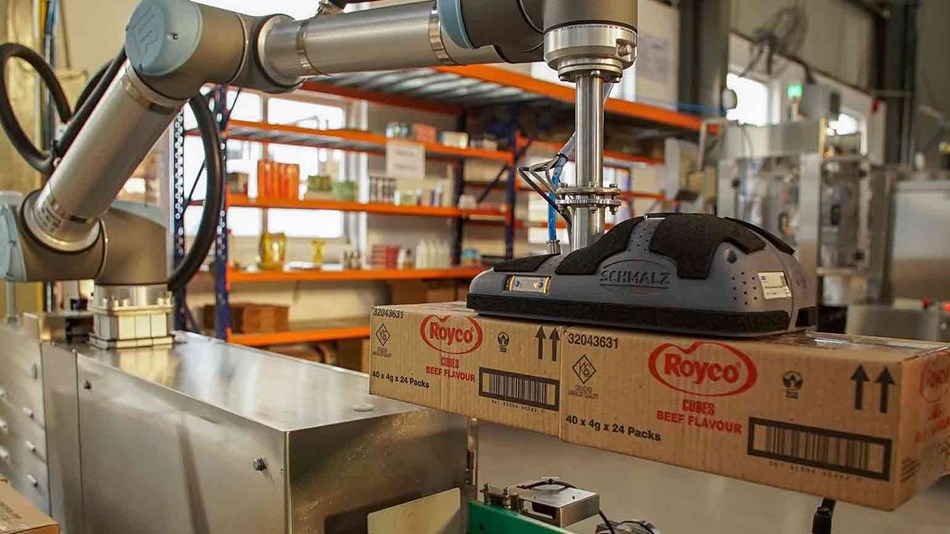
“Most of our customers, while building their manufacturing facility, will not consider space for automated cargo handling. UR’s compact and easy-to-use foot print feature has made automated queuing possible. Cobots also enable a safer and more ergonomic way to handle repetitive tasks like loading and unloading goods.
“When it comes to cobots, our choice is clear, the best solution on the market is Universal Robots. UR, the market leader in this segment, offers uncompromising flexibility with a very good cost-to-quality ratio. Cobots are easily integrated into production lines with minimal accessories. Its lightweight nature also allows it to be transferred from one production line to another using only wheels. These factors result in a faster return on investment,” said Vishnu Puranik, General Manager of Clearpack.
OPTIMIZE STORAGE SPACE
Satisfied with their choice of cobot, the team then searched for the ideal accessory to enhance the queuing solution and allow the cobot to increase stacking height, optimizing storage space in the body. production facility.
Browsing through UR+’s online showroom, the team discovered LIFTKIT, a robotic accessory that can be attached to the base of a cobot, allowing it to be lifted vertically up to 900mm with a possible height. shortened. The team wasted no time contacting SKF Motion Technologies to place an order.
“We were pleased to hear from Clearpack who were interested in integrating LIFTKIT and UR10 for a cargo handling solution. LIFTKIT complements the UR cobot very well, by adding an additional linear axis to expand its range. The UR System is an investment for the customer and LIFTKIT is an accessory that can help maximize this investment in terms of productivity and return on investment.
“The UR+ platform offers a great opportunity to showcase our products to this booming cobots market. It is a very targeted way to advertise our products specially designed for Universal Robots. Feedback has been huge since joining UR+. Thomas Lotz, Business Support Manager, SKF Motion Technologies, said we have never had such immediate market impact and response.
“Since LIFTKIT was designed around UR requirements, it was fairly easy for us to integrate and put the whole system together, taking no more than a day. We looked at different options but with LIFTKIT we were able to get the required stack height at the linear speed we wanted. So it was an easy decision for us. SKF Motion Technologies is also a trusted name in the market that has given us the reassurance to stay ahead of LIFTKIT,” added Vishnu.
UR, through its cobots and UR+ platform in partnership with LIFTKIT, has provided Clearpack with a great solution to meet customer needs. This has led to an increase in orders for palletizing solutions.
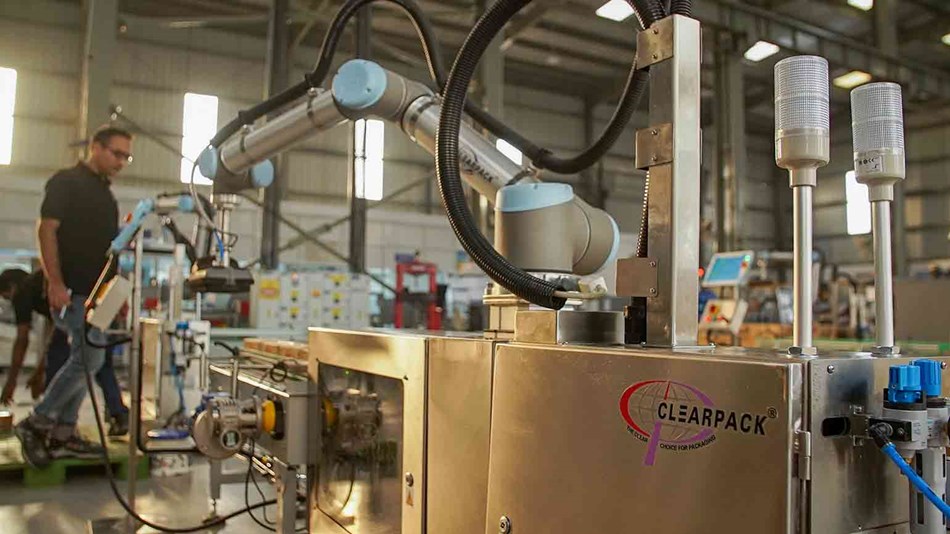