INCREASE ACCURACY AND CONS
UNIVERSAL ROBOTS COOPERATIVE ROBOT ARM CAN REDUCES ASSEMBLY TIME, SPEED UP PRODUCTION AND IMPROVE QUALITY
Establish repeatable, precise assembly processes such as screwing, bolting, assembling parts, and fasteners while reducing frequent injuries in the workplace. With the correct working mechanism of the adaptor, the UR collaborative robot can handle the assembly process of plastic, wood, metal or other materials. If the assembly robot comes into contact with a person, our patented technology limits the force of contact. The user can also program the UR robot to slow down when someone enters the robot’s work area and continue operating at full speed when the person leaves.
Universal Robots provides a cutting edge platform for small businesses looking to optimize production. Thanks to its compact and lightweight design, even with changes in your workflow, you can quickly and easily deploy assembled robotic arms to new product lines. The intuitive software allows even the most inexperienced person to quickly learn basic programming and set waypoints simply by moving the robot into place.
For screwing applications, the coupling on the UR3 offers infinite rotation. The integrated torque/force sensor in the e-Series robot allows the robot to drive screws directly without the need for costly torque control screwdrivers. And the repeatability of the UR robotic arm of +/- 0.03 mm (30 microns) makes the robot ideal for automating fast-precise handling operations.
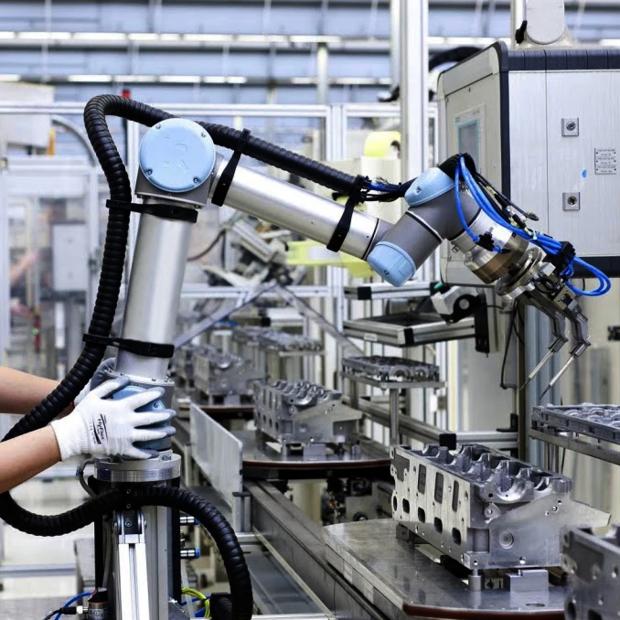
Benefits that Cobot Universal brings when used in assembly applications
- Reduced operational costs: Universal Robots offers all the advantages of robotics automation, without the traditional costs associated with robot programming, setup, and security staffing. The average payback period is 195 days. This is the fastest timeframe in the robotics industry.
- Now you can free operators from dirty, dangerous and tedious jobs to reduce injury and stress from repetitive work. Almost thousands of UR robots worldwide can operate without protection (after risk assessment), right next to the operators.
- Expand production capabilities, while improving production quality, consistency, and speed. It’s quick and easy to deploy robotic arms in new processes, helping you to rapidly improve your ability to automate virtually any manual task, including small-scale manufacturing operations or those that require more attention. rapid change. Robots can reuse programs for recurring tasks.
- The UR robot can be used in most assembly applications. The robot saves space and can be quickly reprogrammed for use with different machines. The extension of the robot can be customized according to your production needs.
- All robots from Universal Robots are IP-54 certified. The robot will need protection when working in corrosive liquid environments.
The company is using Cobot Universal in the assembly line: RUPES
POWER TOOL MANUFACTURER, RUPES, HAS COMMITTED TO REMOVING DEFINITIONS AND WASTE ON THE PRODUCTION LINE, ALWAYS IMPROVING WORKING CONDITIONS FOR THE LABOR. THIS IS HOW THE COMPANY IMPLEMENTED UR ROBOT TO COOPERATE WITH OUR EMPLOYEES, AND INCREASE PRODUCTION CAPACITY.
Challenge:
To be a global leader in sanding and polishing tools, a company must be at the forefront of innovative technologies. Over the past 50 years, RUPES has perfected the manufacturing process, while never compromising on investment in people. In an effort to find smarter and more sophisticated products, RUPES has committed to producing “zero defects” products – and has contacted Universal Robots for an automation solution to strengthen its workforce. excellence, minimizing waste and delivering immediate results.
Solution:
RUPES has deployed UR robots on its production line to perform heavy and repetitive tasks, giving workers time to do more rewarding tasks. Employees find that the robots are easy to use and install and program, and they produce immediate results – maintaining product quality and increasing productivity.
The robot’s versatility means that they are easy to deploy in different areas of the factory and can be quickly reprogrammed to assemble other products, under tight deadlines.
RUPES manufactures power tools, including grinders, sanders and belt polishers, with many small parts. The fastening phase of the assembly is often the hardest – if the screw is not perfectly positioned and tightened to the optimum level, there is a high risk that the product will break and the line will stop production. . The UR robot was able to solve this problem easily, with precise positioning and force control to ensure that every screw was fixed to specification.
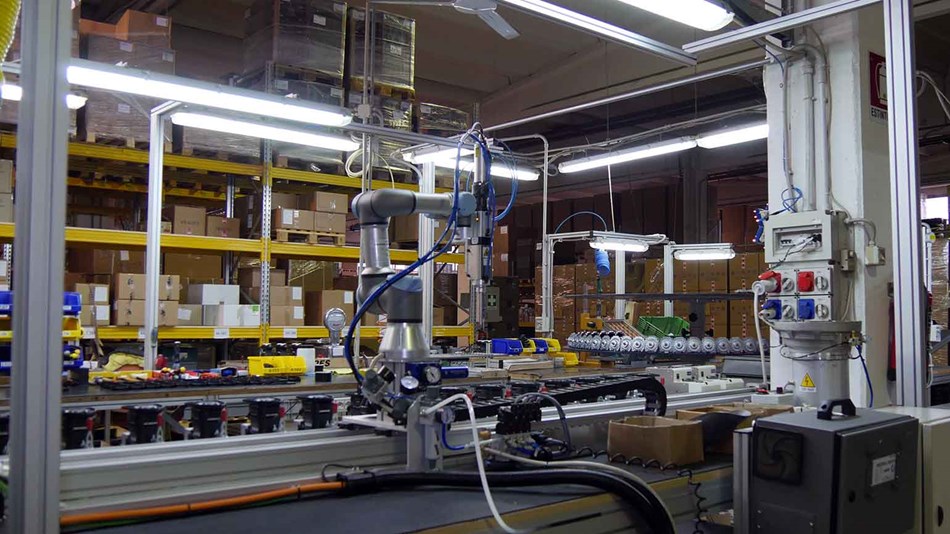
The company also customizes the robot’s advanced safety features to protect employees.
As a result of the successful implementation of this UR robot, RUPES has achieved its commitment to manufacturing “defect-free” products. Now, the company is applying additional collaborative robots to other manufacturing processes.
CHALLENGES IN AUTOMATIC PROCESS SOLIDED:
- Reduce the amount of heavy, repetitive work.
- Increase efficiency and productivity.
- Reduce defects and waste.
- Adapt to different processes.
IMPORTANT VALUE FACTORS:
- Efficiency and performance
- Quality and Employee Satisfaction
- Reduce costs through waste minimization
MISSIONS PERFORMED BY ROBOT COOPERATIONS
- Assemble