UR collaborative robots are used throughout the food and beverage supply chain in a variety of secondary processes such as packaging and feeding. Collaborative robots can work in conditions from humid greenhouses to cold rooms to operate hot ovens, freeing employees from repetitive tasks that can cause injury in unfavorable environments. .
Collaborative robots excel in low-contact processes and can work around the clock without a break. It is ideal during peak seasons, when collaborative robots can meet productivity requirements without the need for additional seasonal workers. Next, flexible, easy-to-program robots can be redeployed to new production lines or to a variety of processes. Without a safety fence (after risk assessment), the collaborative robot-based packaging or production line can be easily reconfigured, delivering added value even when running at low volumes.
For picking/packing/unloading/palletizing applications, the UR collaborative robot models fully meet the reach and payload requirements. Built-in loading/unloading wizard makes implementation easy, even meeting specific customer needs for pallet patterns and labeling that are often required for physical distribution products and beverages.
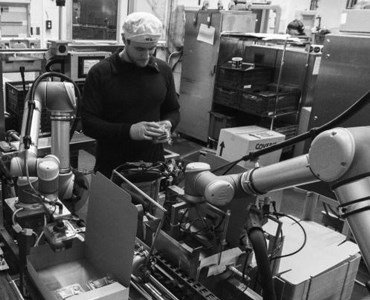
ADVANTAGES OF COLLABORATE AUTOMATIC PROCESS
FLEXIBLE
- Quickly adapt assembly, testing or packaging lines to meet new requirements. Collaborative robots can be programmed and redeployed easily. These lightweight robotic arms can even be mounted on trolleys for greater mobility.
ACCURACY
- Increase quality and uniformity in repetitive jobs where workers face many difficulties. Collaborative robots can reliably perform complex assembly operations, precise gluing, and uniform measurement and inspection procedures without interruption.
Productivity
- Even small and medium-sized electronics manufacturers can afford to buy collaborative robots to boost productivity. Meet competitive demands for faster productivity and lower costs, and typically see ROI in less than a year.
COOPERATIVE ROBOT APPLICATIONS
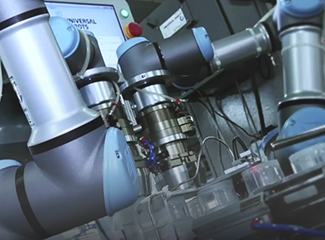
ASSEMBLY APPLICATIONS
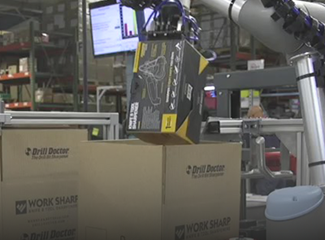
MATERIAL HANDLING APPLICATIONS
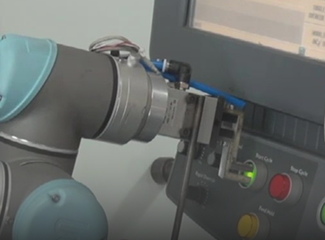
APPLICATIONS FOR LEARNING
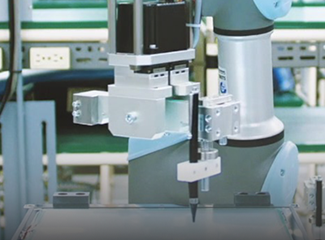
APPLICATION QUALITY CHECKING
CASE STUDY
ROBOT UR10 HELP KUMLA-based ORKLA FOODS COMPANY, CAN ORGANIZE THE PRODUCTION PROCESS AND CREATE STABLE FOR FOOD PACKAGING IN CARTON. ROBOT IS EASY TO INSTALL, EMPLOYEES CAN EASILY LEARN HOW TO HANDL AND OPERATE THE ROBOT. ROBOT WORKS AWESOME IN DIFFERENT NETWORKS OF PRODUCTION MACHINERY, EASILY MOVING AND NO ADDITIONAL SAFETY SETTINGS NEEDED.
Challenge:
On January 1, 2014, Orkla Foods Sverige Group was “born”, after successfully combining three food companies Abba Seafood, Procordia Food and Frödinge, with headquarters in Eslöv, the company has many Currently, these are located in Eslöv, Tollarp, Fågelmara, Frödinge, Kungshamn, Örebro, Vansbro and Kumla.
Among other products, the Kumla factory is responsible for the production of vanilla ice cream. Before Orkla Foods Sweden invested in Universal Robots UR10, bags of vanilla ice cream were hand-packed in cartons. The company’s goal was to find an automation solution that could work with different production machines in the network, could be easily moved and programmed, could work with employees without need additional safety settings.
“An important requirement is that the robot must work perfectly so that we don’t have to have extra supervision or support to keep the robot running. Johan Linné, Area Manager at Orkla Food Kumla, said: “It would be a big plus if the robots didn’t need extra safety protection around them and could work safely with their employees. I.”
Solution:
After taking advice from a local business, the company tested the UR10 and was impressed. The process is automated including the placing of bags into cartons. The robot works independently but is part of a chain of people who pack the cartons, who pack and receive the finished product from a pump. Johan Linné says the UR10 robot simplifies everything in the manufacturing process and helps the company streamline and reduce heavy, tedious and repetitive work for machine operators.
“The robot did a great job,” he summed it up. “It’s flexible, easy to deploy, simple to program, and can perform different tasks in the same network with other machines.”
“An important advantage is that the robot will stop if you hit it, which means the robot is very safe and does not require any safety protection around it, making it easy for the collaborative robot to work. with employees”.
“We currently have a stable, highly economical process, and we are looking at whether this robot has other applications.”
The payback period for the investment in the UR10 is about six months, concludes Johan Linné.