If your device doesn’t work, it costs you money. While machine care positions are often difficult to fill and maintain, collaborative robots work continuously. Collaborative automation, ideal for machine-care applications such as CNC and pressure casting machines, presses and rotary tables, can run around the clock in a uniform and reliable manner. You’ll be able to keep your workshop afloat and possibly move skilled mechanics into higher value and more rewarding positions.
Collaborative robots are also at the heart of collaborative welding systems that are a fraction of the cost of traditional automation systems and can accommodate standard welding jobs. Automate small or repeatable products that welders don’t want to do and move your best welders to more profitable product lines. The result is more consistent quality and greater employee satisfaction.
Collaborative automation is affordable and flexible, so you can easily move robotic arms from job to job as your business needs change. Programming is quick and easy, and programs can be saved for quick changes. No more downtime and no more scrap when you train new and seasonal workers. And no more quitting jobs because of limited resources.
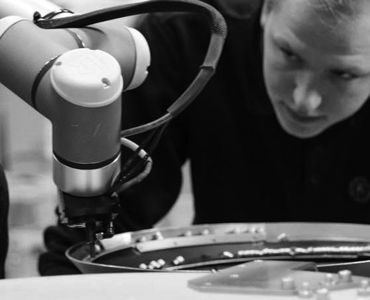
ADVANTAGES OF COLLABORATE AUTOMATIC PROCESS
FLEXIBLE
- Quickly adapt assembly, testing or packaging lines to meet new requirements. Collaborative robots can be programmed and redeployed easily. These lightweight robotic arms can even be mounted on trolleys for greater mobility.
ACCURACY
- Increase quality and uniformity in repetitive jobs where workers face many difficulties. Collaborative robots can reliably perform complex assembly operations, precise gluing, and uniform measurement and inspection procedures without interruption.
Productivity
- Even small and medium-sized electronics manufacturers can afford to buy collaborative robots to boost productivity. Meet competitive demands for faster productivity and lower costs, and typically see ROI in less than a year.
COOPERATIVE ROBOT APPLICATIONS
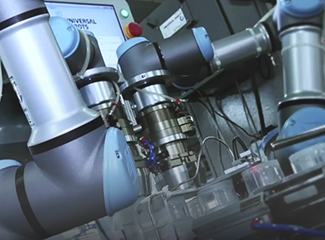
ASSEMBLY APPLICATIONS
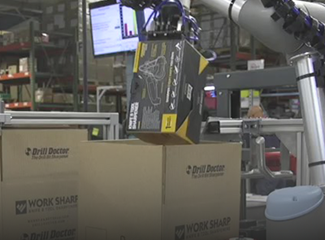
MATERIAL HANDLING APPLICATIONS
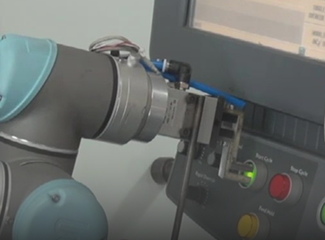
APPLICATIONS FOR LEARNING
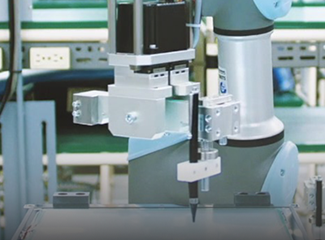
APPLICATION QUALITY CHECKING
CASE STUDY
Cobot UR is popular in metal and mechanical applications. Choose from one of our robotic arm products, available in a variety of payloads, reach and sizes. Model UR5 Collaborative Robot is one of the favorite products in machine care and welding applications. Read and explore the following research articles to find your next automation opportunity.
WITH ROBOT UR10, LEAX GROUP IS NOW PROFIT FROM A VERY FLEXIBLE RESOURCES THAT CAN MOVE BETWEEN BETWEEN THEIR 11 FACTORIES AS NEEDED. FOR THE GROUP, ROBOT ARM IS A LONG-TERM INVESTMENT FOR FUTURE CHANGING PRODUCTION REQUIREMENTS IN THE PRODUCTS LIST.
Challenge:
The LEAX Group, a contract manufacturer in Sweden, often moves machines in the factory to find the best production line. Sometimes, entire production lines are shipped to other sites at LEAX. Therefore, the automation solution the company is looking for must be flexible, easy to program, and make efficient use of space.
“We manufacture everything from small annual volumes up to 100,000 units of a specific order per year. It is extremely important to us, which is also one of the strengths of the company, that we can quickly fulfill orders for new products. We have very high requirements on start-up time for a unit,” said Rickard Isaksson, Quality Manager at LEAX Group.
Solution:
LEAX Corporation has decided to invest in three UR10 robotic arms. They are used for changing pieces in the cutter and for loading and unloading two tooth cutters with a three-finger grip.
Rickard Isaksson explains that the UR10 from Universal Robots is a long-term investment: “If you compare the UR10 with a normal machine, the payback is 18 months, assuming the operator works two shifts. However, that is too narrow a perspective to consider only the payback period. Let’s say in three years we will stop producing a certain product. We can then reuse the UR10 with new and different applications. If we’ve designed an extra feature specifically for a certain product, we’ll need to go back to where we started again.”
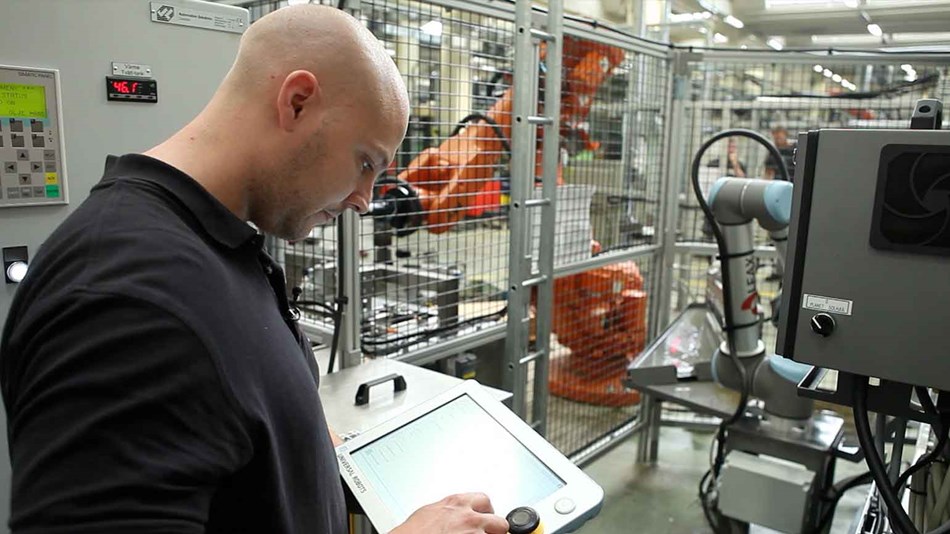