In this fast-paced industry, agility is the key to competitiveness. Whether you’re building assembly line assemblies, loading and unloading test parts, or sorting and packaging products, flexible collaborative robots can improve productivity, quality, and uniformity.
Safe with workers (after a risk assessment), collaborative robots can handle precision jobs such as assembly, weighting, screwing or labeling with very high repeatability. By automating these repetitive processes, you can reallocate skilled workers to more valuable jobs. Collaborative robots are also an ideal way to create distance between workers on the production line, by filling entire processes.
Collaborative robotic arms are lightweight and easy to program, so they can be easily moved from one production line to another—or from production to packaging or loading/unloading/ onto pallets—when needed. Even in the competitive electronics manufacturing industry, collaborative robots can provide a return on investment in less than a year.
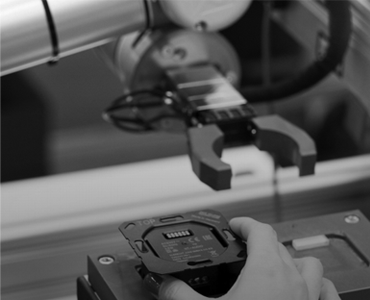
ADVANTAGES OF COLLABORATE AUTOMATIC PROCESS
FLEXIBLE
- Quickly adapt assembly, testing or packaging lines to meet new requirements. Collaborative robots can be programmed and redeployed easily. These lightweight robotic arms can even be mounted on trolleys for greater mobility.
ACCURACY
- Increase quality and uniformity in repetitive jobs where workers face many difficulties. Collaborative robots can reliably perform complex assembly operations, precise gluing, and uniform measurement and inspection procedures without interruption.
Productivity
- Even small and medium-sized electronics manufacturers can afford to buy collaborative robots to boost productivity. Meet competitive demands for faster productivity and lower costs, and typically see ROI in less than a year.
COOPERATIVE ROBOT APPLICATIONS
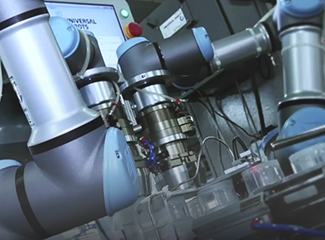
ASSEMBLY APPLICATIONS
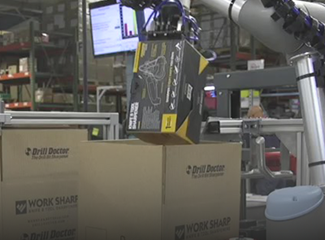
MATERIAL HANDLING APPLICATIONS
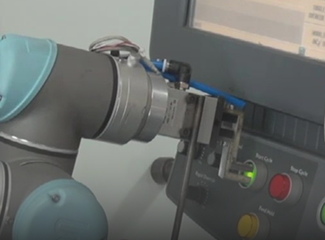
APPLICATIONS FOR LEARNING
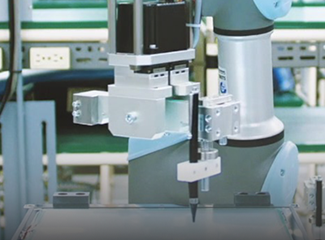
APPLICATION QUALITY CHECKING
CASE STUDY
UR Collaborative Robots are used in electronic applications worldwide, from transferring FOUP in the silicon industry, to assembling, inspecting and packaging electronic products in most industries.
CHOOSE AND ORDER EASY GLASS TUBE WITH FLEXIBLE COBOT
Challenge:
The company’s plan is to automate the monotonous task of a glassworking machine, deploying skilled workers to more complex jobs to improve production processes. Therefore, the robots will be tasked with handling fragile glass tubes, which requires a very high level of precision. That’s why CEO Hofmann Glastechnik decided to deploy two robots from Universal Robots.
“Glass products are very fragile. Even the smallest temperature fluctuations of the instrument can affect the results. In the past, our workers made the fiberglass cutters by themselves. Disruptions in the production process, even for a short time, cause machines to experience several drops in temperature. When we used the UR collaborative robot for the first time for this work, we achieved excellent results,” says Robert Hofmann, CEO of Hofmann Glastechnik GmbH.
Solution:
Two robotic arms UR5 and UR10 work at some CNC fiberglass cutting machines. They machine cutters up to 11 hours per day. If necessary, the company can flexibly deploy the robots to other fiberglass cutters. As a result, the company developed a facility that allows them to switch the UR robot between different machines without any problems. The robots are immediately ready to go after the settings have been changed in this way. Björn Uthe, Machine Area Manager at Hofmann, is also convinced by the usefulness of the UR robot. “The UR robot interface is very intuitive. Once you understand the processes and functions involved, anyone can operate these robots.” Thus, the robotic arm also reduces the workload for skilled workers at Hofmann. “The UR robots have made our job much easier. In the past, we had to go back and forth between fiberglass cutters, concurrently doing glass casting all day. We can hardly keep up with the production schedule. With the UR5 and UR10 working with us now, I have more time to set up multiple machines,” explains Björn Uthe.

By using a flexible robotic arm, Hofmann can not only deploy skilled workers for more sophisticated, complex jobs, but also to stabilize production processes and reduce downtime. As a result, both the quality of the glass components and the efficiency of the company have improved significantly. So the company was able to increase the production capacity in the specific application area by 50%, and the initial investment in the robot paid off in about 6 months.