Although the level of automation in the auto industry is currently very high, there is still room for growth. Collaborative robots (Cobots) are driving new efficiencies across the industry, in applications including machine loading, inspection and assembly in powertrain, electronics and furniture manufacturing.
From tier 1 OEMs to contractors throughout the supply chain, cost-effective, flexible Collaborative Robots are improving productivity and uniformity for a wide range of assembly line assemblies, modules and systems. Collaborative robots that are easy to deploy and redeploy are well-suited to optimizing industry customization and responsiveness to changing consumer needs.
Collaborative robots can work alongside workers, increasing their productivity and improving their uniformity, and allowing them to support more of the production line process than in one workspace. only. While traditional automation requires a holistic or no-implementation approach, collaborative robots allow automakers to automate specific tasks and see fast ROI. fast.
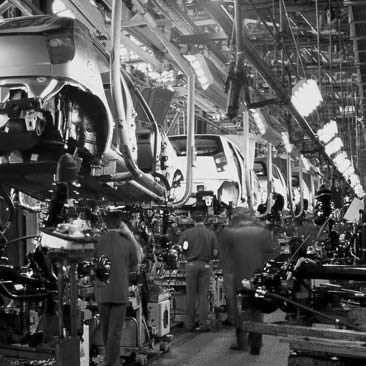
ADVANTAGES OF COLLABORATION AUTOMATICALLY
FLEXIBLE
- Adapt the assembly line quickly and at a reasonable price to new requirements. The lightweight collaborative robot arm can be programmed and redeployed easily and can even be mounted on a trolley for increased mobility
Productivity
- Add new functionality without changing costs to the production line. Meet competitive demands for faster productivity and lower costs, even in processes that are not normally suited for automation.
Evenness
- Increase quality and uniformity in repetitive jobs where workers face many difficulties. Collaborative robots can work continuously while operators focus on higher-value jobs.
COOPERATIVE ROBOT APPLICATIONS
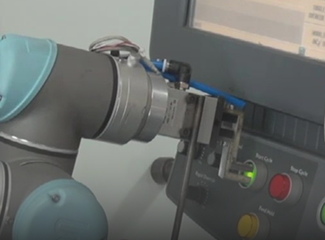
APPLICATIONS FOR LEARNING
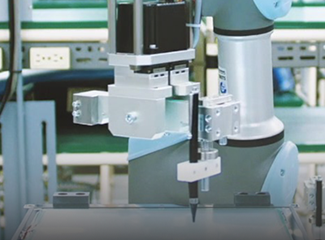
APPLICATION QUALITY CHECKING
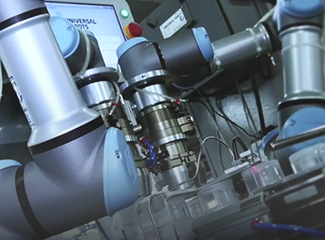
ASSEMBLY APPLICATIONS
CASE STUDY
FIND OUT WHY THE THIRD BIGGEST MOTORCYCLE MANUFACTURER IN THE WORLD CHOOSE TO USE ROBOT COOPERATION FROM UNIVERSAL ROBOTS
Challenge:
Vikas Sawhney, General Manager of Engineering (Robotics and Automation) at Bajaj Auto, said of the automation advancements in the manufacturing industry over the past few decades: “In 2010, we found looking for solutions to automate the company’s assembly lines,” “Two-wheel assembly lines are labor-intensive, difficult to save space, and they require a lot of high-precision physical movements . While trying to automate these assembly lines, one of the basic requirements to have is standardization. Furthermore, we also want to better respond to the needs of the female workforce in Bajaj.”
While the standardization of models is a key factor for Bajaj’s success in the market, the company needs to rapidly expand its production capabilities to accommodate the growing scale of many models and the number of vehicles. to be offered in the market. The key to finding a standard automation solution that is widely deployed and can be leveraged by Bajaj workers for productivity, flexibility and reliability.
“After thoroughly researching the options available on the market, Bajaj Auto selected Universal Robots, primarily based on the collaborative nature of the robots. Key benefits from Universal Robots products such as compactness, short payback period, flexibility, light weight, cost effectiveness, accuracy and safety are what convince Bajaj Auto of Universal Robots’ suitability for standardized processes,” added Vikas.
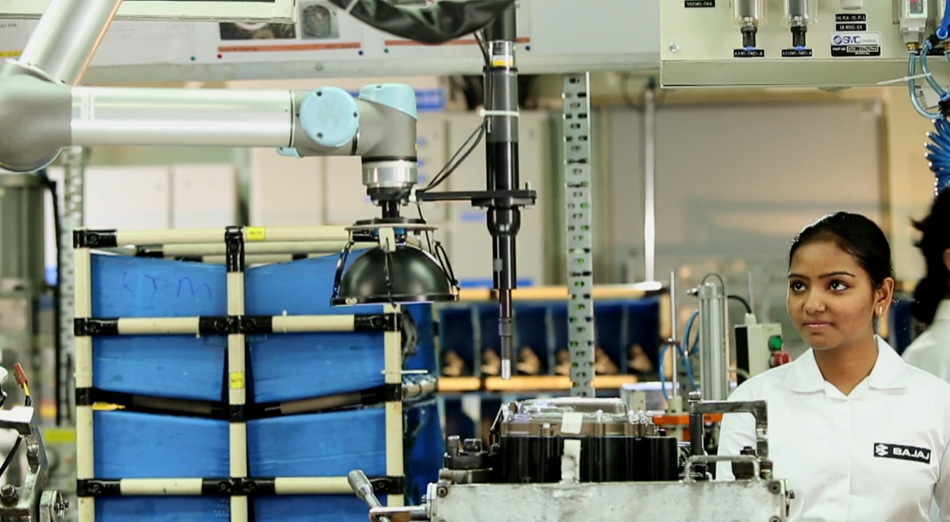
Solution:
After 3 months of extensive testing of Universal Robots cobots at its facilities, Bajaj Company implemented our cobot as a standard solution for all corporate functional requirements. Some processes such as material handling and machine maintenance have been solved by coordination between the cobots and Bajaj staff. Furthermore, new decal applications are now patented by Bajaj. These apps were created by the company to take full advantage of the flexibility of cobots.
Other benefits such as no annual maintenance costs, energy savings and intellectual property retention in the company also contribute to the growth of the organization. In addition, nearly 50% of Bajaj’s workforce are women working on this assembly line.
CHALLENGES IN AUTOMATIC PROCESS SOLIDED:
- Minimize space constraints in a manufacturing facility by using ceiling-mounted cobots.
- Reduce redundancy by completing repetitive but precise normalization operations.
- Supports mixed model adaptability.
- Take on top tasks that require flexibility, productivity, and reliability.
- Reduce the workload for female workers.
IMPORTANT VALUE FACTORS:
- Interoperability
- Compact, lightweight and extremely versatile
- Safe, with 30 patented limited features, built to ISO TS 15066
- Ceiling, wall or floor mount – no modification required
- Lowest running costs – ultra-low power consumption and no need for an additional property management company
- Can operate without safety barriers (according to application risk assessment) in areas with limited space
TASKS PERFORMED BY COOPERATIVE ROBOTS:
- Material handling
- Maintenance machinery
- Decal application
- Polish
- Visual applications
- Screwdriver
- Application Sealant
- Weld