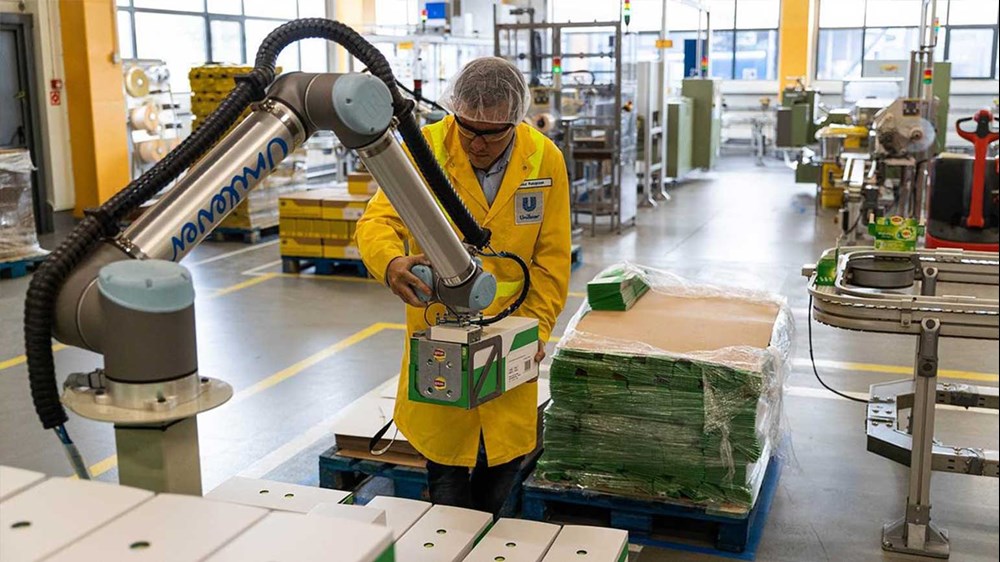
Packing and loading/unloading pallets is one of the most stressful and musculoskeletal applications for workers in the supply chain. Lifting heavy objects and bending over to lift or wrap are not only ergonomic (unconvenient to the body) movements that pose a risk of injury, but are also repetitive, which can lead to human error when concentration is reduced. The combination of these factors makes the robotic arm of the collaborative robot the ideal partner for packing & picking processes.
With robotics technology delivering quick ROI, we’re getting a lot of interest from customers looking to tackle production issues caused by the COVID-19 pandemic. Faced with a spike in demand for products such as medical components and PPE, some customers have found that our cobot palletizing and palletizing technology is a means effective way to increase productivity.
Similarly, restrictions caused by COVID-19 are exacerbating pre-existing labor challenges in manufacturing and other industries. Never before has finding a source of labor been so difficult; the problem of workers absent due to illness is a real risk; and travel restrictions coupled with social distancing practices may make adding workers unfeasible in the short term. In these situations, autonomous robots can solve problems, replenish labor shortages, and ensure uninterrupted business operations, despite general operating conditions and unfavorable workforce situations. profit.
COBOT CREATES NEW LABOR DEMAND:
In some situations, deploying cobots to do the packing and palletizing and unloading can even lead to hiring new workers thanks to increased production levels. This happened with RNB Cosméticos in Spain. This company has integrated 6 Ur10 robot arms of Universal Robots into its wrapping and packaging workshop to perform the loading/unloading of pallets at the end of the line. After the automation robot integrated production line was established, RNB Cosméticos was able to increase production quickly and efficiently.
Working with humans in 6-pack-per-minute production cycles and adapting to more than 350 different items, the system is so efficient that the company has hired new workers to handle the increased production leap. At the same time, existing workers have been released from tasks that are not ergonomically appropriate to focus on improving their professional skills. Instead of packing and loading and unloading goods, workers are now responsible for managing the cobot’s operations. “We do not hire experts to handle high-tech robots. We are turning our employees into experts by enhancing their expertise,” shared Aurelio Tornero, General Industry Manager of RNB Cosméticos.
COBOT HANDLING L’ORÉAL .’s Heavy Lifting Problem:
At L’Oréal India’s Pune plant, operations at the packagingline are done manually, with operators having to lift approximately 8,500 kg of product in each 8-hour shift. L’Oréal India recognized this as too great a risk for the operators and deployed two UR10 robotic arms to take over the job. Cobot has helped the company to completely eliminate human labor in the stage packing and loading/unloading of pallets, and at the same time, improving overall equipment efficiency in the factory by 5% by saving time on changing pallet replacement. “The collaborative robot has completely eliminated the risk of ergonomics. They are user-friendly, maintenance-free, and extremely efficient. We are really satisfied using Universal Robots cobots,” shared Ranjit Ekda.
NIPPON ZETTOC MIX THE BEST CHARACTERISTICS OF HUMANS AND ROBOTS INTO THE PRODUCTION LINE:
In Japan, the leading original parts manufacturer (OEM) for toothpaste, NIPPON ZETTOC, adopted cobot UR5 to solve the problem of labor shortage on their packaging and canning lines. Mr. Junichi Kano, Manager of Manufacturing Technology Department of NIPPON, said, “Human labor has the advantage of being flexible, but of course there are negative points such as they can suddenly quit their job and lack of a number skills. So our goal is to create a production line that combines the best features of humans and robots.” The company’s inner box packaging line that used to require two people now requires just one person and four UR5 cobots, allowing for continuous production when workers take breaks. The UR5 robotic arm also helps speed up production, increasing the number of products packed per hour by 30%. The outer box packing line is now fully automated by the UR5, while workers spend their time on more value-added tasks such as material feeding and process inspection.
FAVORITE PALLET UP/DOWN LOADING GUIDE:
Ease of use is a trait that Universal Robots strives to ensure in all its solutions. To simplify programming for pallet loading/unloading tasks, we’ve included a special picking wizard in Polyscope OS. The wizard allows the user to simply specify where the corners of the box are and add dimensions, while the robot arm will figure out where to put the parts in the right place.
Specialized aerospace components manufacturer Tool Gauge used our loading and unloading wizard to reduce labor costs, while freeing workers from repetitive and time-consuming tasks at the factory in Seattle, USA. Initially, an easily damaged copper machined part was manufactured by a skilled CNC machinist. This person will pull the parts out of the CNC chute, clean, rinse, dry, and box. Now, a UR3 cobot will take the parts out, put them in a clean sink, put them in front of the dryer, and then drop each part into individual cardboard boxes in a grid pattern.
Steve Ouzsts, manufacturing engineer at Tool Gauge, explains, “The loading and unloading wizard is really cool, it’s both effective and easy to do.” Tool Gauge’s general manager, Jim Lee, estimates that the company saved $9,000 USD in labor costs on the first order. “We can no longer waste the talent of our machinists, but can let them focus on higher value projects like installing and programming CNC machines,” he explains.