I. Problem:
The customer is using a manual weighing and data logging system and the system is labor intensive to handle weighing and data recording and has the potential for confusion and inaccuracies, affecting productivity work of workers and factories, causing the factory to suffer great losses every month.
In addition, the current model of productivity monitoring has several major problems:
The system needs 1 employee to weigh and 1 staff member to sit at the table to record the weighing data on paper, then summarize and send it to the accounting department at the end of the day => labor cost.
The system does not have historical data information that records the entire working process of workers. => do not properly access and evaluate the capacity of employees.
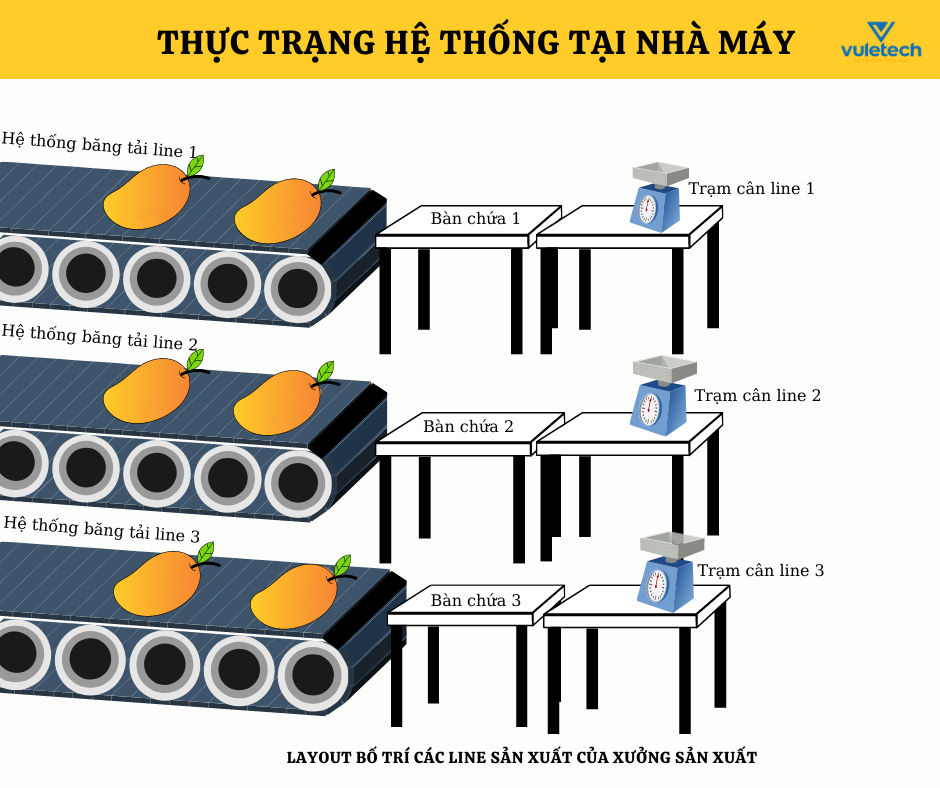
II. System requirements:
The weighing & data management system needs to meet the following requirements:
The system is capable of integrating and connecting with existing devices.
Ensure accuracy within the capabilities of existing weighing systems.
Ensure objectivity and confidentiality of weighing results.
Effective, reducing investment costs in human resources to monitor the system.
Weighing data will include historical data images, allowing re-query when needed.
Waterproof, anti-rust, ensure food safety and hygiene. Easy to clean.
The device can withstand high humidity.
III. VULETECH's proposed solution:
- Paradigm:With the problems encountered by customers as well as actual surveys at the factory, Vu Le proposes a model of automation solutions for the system as follows:
After the fruit is peeled and finished, the operator will bring it to the Scales to weigh and calculate the kilogram and the amount of a worker. The data is then processed through IPC Beckhoff and a computer with integrated i-MAG intelligent factory management system. In addition, there is a TV/Dashboard screen (flexible location) so that the Manager can monitor the productivity of workers as well as the production line.
Through the Router in the factory, the data will be transmitted quickly so that the manager can monitor the actual working status of the production system, thereby making appropriate decisions to keep up with the requirements. solve the situations that occur, help the factory achieve high productivity, produce better products.
2. Một số hình ảnh của hệ thống này:
IV. Advantages of weighing and billing systems for the dried food industry:
Productivity increases rapidly
Tracking productivity along with minimizing downtime is always the goal of iMAG. Controlling all operations of production equipment and reporting parameters to decentralized users is one of our strong points
Raw material waste monitoring
In the process of rudimentary production, or the input materials have not been controlled
Monitor machine performance
When the equipment in the machine works for a long time, it may reduce production efficiency
Energy Saving Energy Monitoring
Statistics related to the use of electricity, water, petrol, gas, ..
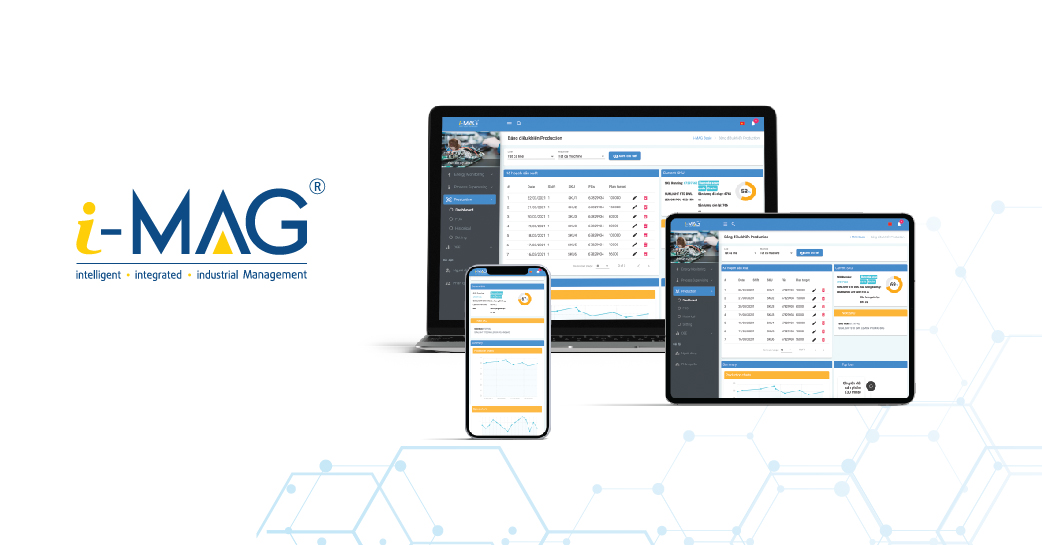
With the use of i-MAG smart factory management software, managers can plan management strategies, measure parameters via sensor systems or IoT devices, and analyze data in real time. Real-times
Real-time production monitoring
Control volume, output quantity compare with rated output
Monitor cause of machine stop
Control and predict equipment that is likely to fail during production
Machine maintenance management
Create a list of spare-part equipment, remind machine warranty time
Cost control
The waste of materials and energy always comes from unnamed causes, controlling this loss with iMAG can bring huge profits up to billions of dong for businesses.
Daily automatic report by email
Ability to retrieve data when needed.
VULETECH specializes in providing solutions for checkweigher machines. For more detailed information, please contact:
Vu Le Technology Co., Ltd
Address: 27 Xuan Quynh, Gia Hoa Residential Area, Phuoc Long B Ward, City. Thu Duc, HCMC
Hotline: (028) 3620 8179 / 3620 8176 / 3620 8177
Fax: (028) 3620 8178
Mail: info@vuletech.com